It is with great joy that we celebrate the 25 years of TECNOLITA of our employee Dirce Ogawa, who throughout this time has been strengthening and consolidating the company, with her work and dedication.
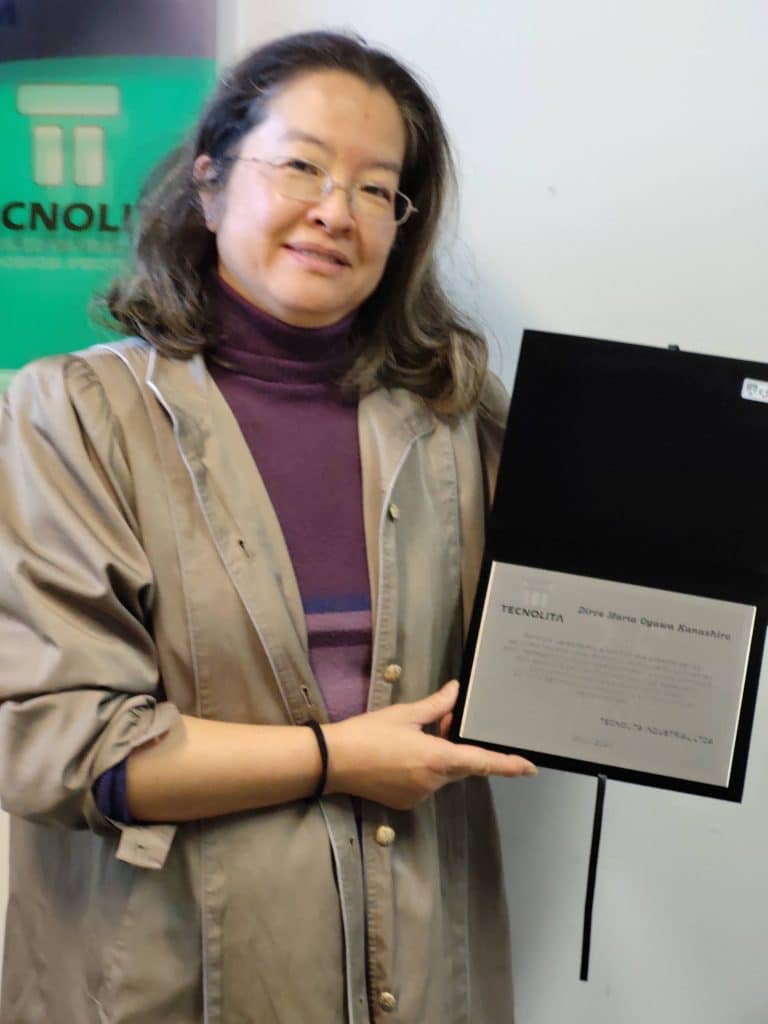
It is with great joy that we celebrate the 25 years of TECNOLITA of our employee Dirce Ogawa, who throughout this time has been strengthening and consolidating the company, with her work and dedication.
In the second half of 2018, TECNOLITA was consulted by a customer who owns a 140 ton capacity three-phase electric arc furnace.
This furnace operates without opening the vault, as the preheated metal scrap is loaded through a metallic conveyor and the pig iron
is fed into the electric oven through a transfer chute. This customer’s complaint related to the low performance of the delta used.
We found that our client used a delta, which was installed inside a water-cooled metal ring.
The average delta campaign was in the order of 80 races, what caused to having to switch it every week.
The operational interruptions for welding the refrigerated ring tubes that punctured during operation and the successive changes of the
deltas provided high levels of power off and low productivity.
This information were sent to TECNOLITA’s Engineering Department, which started to develop a new project that contemplated the
following conditions:
1- Use of dry metal ring without water cooling;
2- Modification of the refractory profile in order to better adapt to the electric oven;
3- The adaptation of the refractory part to the existing operational model.
After 6 months of work, monitoring of tests, analyzes and modifications in the original project, we were able to produce, install and
operate a delta, which obtained a campaign of 655 runs, operating for more than 40 days without any interruption.
The final results of this development can be seen in the table below:
MAGNECO METREL INC., An American company, produces and distributes special monolithic refractories linked to colloidal silica for applications in the steel, cement, aluminum, ceramic, copper, ferroalloys, foundry, glass, etc. industries.
The company, founded in 1978, is based in Addison, Illinois and has plants in Addison, Illinois; Negley, Ohio; Gary, Indiana; Tianjin, China and Shildon, England.
Metpump® products, developed by her, are used “in situ” through applications for pumping, projection, injection and even pouring. It also allows special parts to be obtained so that the coating assembly is even faster and more efficient and with excellent dimensional quality.
Metpump® products are materials that allow drying and sintering in a very short time, since all the free water in the material is removed at a temperature of 120ºC.
Worldwide, the Metpump® brand is synonymous with quality, speed, safety, ease of application and recovery of
refractory linings, as it has provided its customers with quick returns, reduced equipment downtime for their recovery and
increased performance.
From April / 2019, with this partnership formed, TECNOLITA will become the official distributor of MAGNECO METREL products in the Brazilian market and for that, TECNOLITA will have in its stock of a variety of products that can meet this demand.
In parallel to the distribution, TECNOLITA will produce in its factory in Campinas, SP, special parts with Metpump® products, for this our employees are already being trained by MAGNECO METREL technicians to be able to obtain special parts with the necessary quality for each type of application.
With this, the Brazilian market will have at your disposal a fast, safe service, with lower cost and with the quality of TECNOLITA special pieces that the market has already become accustomed to observing. To learn more about this new product line and its applications please contact us.
Contact Center: (19) 3729-3070
Every year, the Pulp and Paper factories schedule their general shutdown for maintenance of their mills in advance, helping the planning of suppliers in this process. The areas involved for maintenance are the fiber line, recovery and utilities, drying and raw material. Thus, every year TECNOLITA seeks to further strengthen its relationship with customers, participating in the stops with the supply of quality anti-corrosion materials and specialized labor. In 2014 TECNOLITA was present in the stops of seven different factories, being them : Fibria – Jacareí / SPSuzano – Limeira / SPKlabin – Telêmaco Borba / PR *Klabin – Otacílio Costa / SC *Klabin – Correa Pinto / SC *Cenibra – Belo Oriente / MG *International Paper – Luis Antonio / SP * All works were executed in accordance with the best techniques and within the pre- established deadline. TECNOLITA’s quality materials and the experience the company has in the Pulp and Paper business ensure customer satisfaction with the service provided. For this year 2015 we hope to maintain the partnership with the customers we already serve and increase our presence at the stops factories, always looking to meet your needs with the best cost-benefit of the market. If you have already established the date of the maintenance stoppage of your Pulp and Paper plant, please contact us. TECNOLITA has been in the market for 23 years and is a reference when it comes to anticorrosive coating.
*We have a partnership with Bunker Engenharia Anticorrosiva, a company specialized in the application of coatings, which was responsible for the application of TECNOLITA anticorrosive materials in these works.
CMPC / VALMET – Guaiba 2
In July 2014, TECNOLITA Industrial signed a contract with Valmet Celulose, Papel e Energia Ltda. referring to the “Expansão Guaíba 2 – Fibras Line” project, by the final client CMPC – Celulose Riograndense in Guaíba, RS. In this project, TECNOLITA supplied all the necessary anticorrosive materials and our partner Bunker Engenharia Anticorrosiva was in charge of the execution of the work. Four new bleaching towers were covered, totaling an area of 5,352 m². The work is in its final stage of application.
KLABIN / ANDRITZ 2015 – Puma Project
In January 2015, TECNOLITA Industrial, together with the partner Bunker, closed another major anti-corrosion coating project in bleaching towers. Andritz Brasil is responsible for the work in Ortigueira, PR and the final customer is Klabin. TECNOLITA developed the project for the coatings and will supply all the materials for the protection of the three towers, which will be assembled with the specialized labor of Bunker. The project, called “Klabin-Puma Fiber Line Area”, will cause the company to double its production by 2016 and will have a total coated area of 3,252 m².
The technical staff of TECNOLITA Industrial has successfully participated in most of the major projects carried out in Brazil in recent decades. The Guaíba 2 and Puma projects add more value to our building works curriculum and for the name that TECNOLITA already has in Pulp and Paper sector.
We thank our customers Valmet and Andritz for their trust in the quality of TECNOLITA anti-corrosion materials and the seriousness with which we develop our work: always focusing on customer satisfaction, from the first service to the completion of the works and after-sales.
In November 2015, we received at TECNOLITA Mr. Daniel Quittek, Export Manager at VFF – Vereinigte Füllkörper-Fabriken, a company located in Germany and the largest manufacturer of fillings in Europe.
Mr. Daniel Quittek gave a complete training on Fillings for process columns and catalyst bed supports produced and supplied by VFF.
The entire TECNOLITA commercial team was present at the training, which covered everything from technical and commercial information on the product to the main segments and market opportunities.
Mr. Daniel Quittek ceased all the doubts of our team, leaving us even more qualified to introduce this high quality brand in the Brazilian market.
We had years filled with challenges, achievements, development and growth. Nothing would be possible …
Coatings that combine reinforced plastic applications with special low-porosity ceramics are the highlight of TECNOLITA Industrial’s work (Campinas, SP) at the Horizonte Project, at Fibria Três Lagoas (Três Lagoas, MS).
The coatings used in the factory’s three bleaching towers are the second largest application in the world of this type of product.
Already in operation, the new pulp mill for the production of Fibria Três Lagoas (Três Lagoas, MS), formerly VCP Três Lagoas, combines the use of composites coverings with vinyl ester resin, reinforced with fiberglass blankets, with the application ceramic tiles in a total area of 4,200 square meters of tiles. It is the second largest set of bleaching towers in the world – 67 meters high, second only to the 70 meter SPC towers (Mucuri, BA), also protected by TECNOLITA Industrial.
The cellulose pulp bleaching stage takes place in three towers three towers of calendered steel plate with a conical bottom. In these towers, the cellulose mass is subjected to the presence of hydrogen peroxide, hydrochloric acid and sulfuric acid, in order to, as the name says, be bleached. The mass, very abrasive, is in constant motion inside the towers. It was necessary to apply an internal anti-corrosion coating to the steel structure and to the upper rail, assembled later.
For the anticorrosive coating of the structure, Andritz (Curitiba, PR), the company responsible for the installation, subcontracted the coatings company TECNOLITA Industrial (Campinas, SP), which used coatings based on ester-vinyl resin and fiberglass blankets. For protection against abrasion, imported ceramic tiles with low moisture absorption content were chosen. These plates were installed
manually, with several pieces at key points specially molded, in order to withstand the passage of the dough for several years.
Due to its size and complexity, the application of coatings on 67m high towers was done through an internal motorized structure. The first phase of the coating work consisted of abrasive blasting, for the preparation (treatment) of the surface. Sandblasting is carried out on both concrete and steel, and serves to remove impurities and create an adequate substrate roughness profile for anchoring the first primer phase, already in ester-vinyl resin. This primer then takes several layers of fiberglass mat laminated with resin. Finally, ceramic tiles are laid and grouted.
Extruded ceramic plates and pieces with “swallowtail” claws on the underside, imported ceramic plates stand out for their very low porosity, a factor that minimizes the friction generated by the flow of cellulose. The creation of special and differentiated pieces, produced according to the individual characteristics of each project, provide the final finish to the set. An example is the outlet for the trough, in which the ceramic pieces have a “J” shape, for greater resistance and tightness. Another example is the leading edge of the tank, in its conical part.